Effective change management is important in the manufacturing industry where IT is deeply embedded with operational technology (OT). The risks involved are high because any interruption in IT directly affects production lines leading to expensive downtime and potential safety issues. In this context, AI has become a game-changer, providing unprecedented efficiency, accuracy and predictability to changes. Here are three ways AI is transforming change management for manufacturing companies.
1. Predictive Risk Assessment
As far as changes in IT and OT systems are concerned, traditional change management often depends on manual assessments as well as historical information so as to evaluate possible risks linked with such alterations. This can be time-consuming and prone to error by humans though. Conversely, Artificial Intelligence can examine massive volumes of data rapidly enough to identify patterns and relationships that may not be obvious to human analysts.
AI in Action:
- Predictive Analytics: With reference to historical data and real-time monitoring, AI models can forecast the probability that a prospective change will contribute a problem For instance, if there were previous instances when machine performance was disrupted during a software update, the AI system alerts of such risk before implementing the changes.
- Scenario Simulation: AI is capable of simulating different scenarios for understanding the pre-effects of the changes. The simulations show the manufacturer what are the potentials for failure and the remedial plans to take prior to the time of failure. This will make the transitioning smoother and with minimum hit.
2. Automated Change Approval Processes
In the case of manufacturing and other complex IT organizations, the change approval process is linked with numerous stakeholders and has strict change protocols. Any delay caused by this process results in a bottleneck and directly affects productivity. Here also comes the play of AI into the picture with the optimization of change approval workflow. Therefore, faster and firmer decisions can be ensured.
AI in Action:
- Unifying Siloed ITSM Data: Leveraging our knowledge agents, Accrete’s ITSM product sifts through, standardizes, and connects like-data together to show clear knowledge graphs, or dependency maps, which shows interconnected data around specific IT assets, incidents and change tickets.
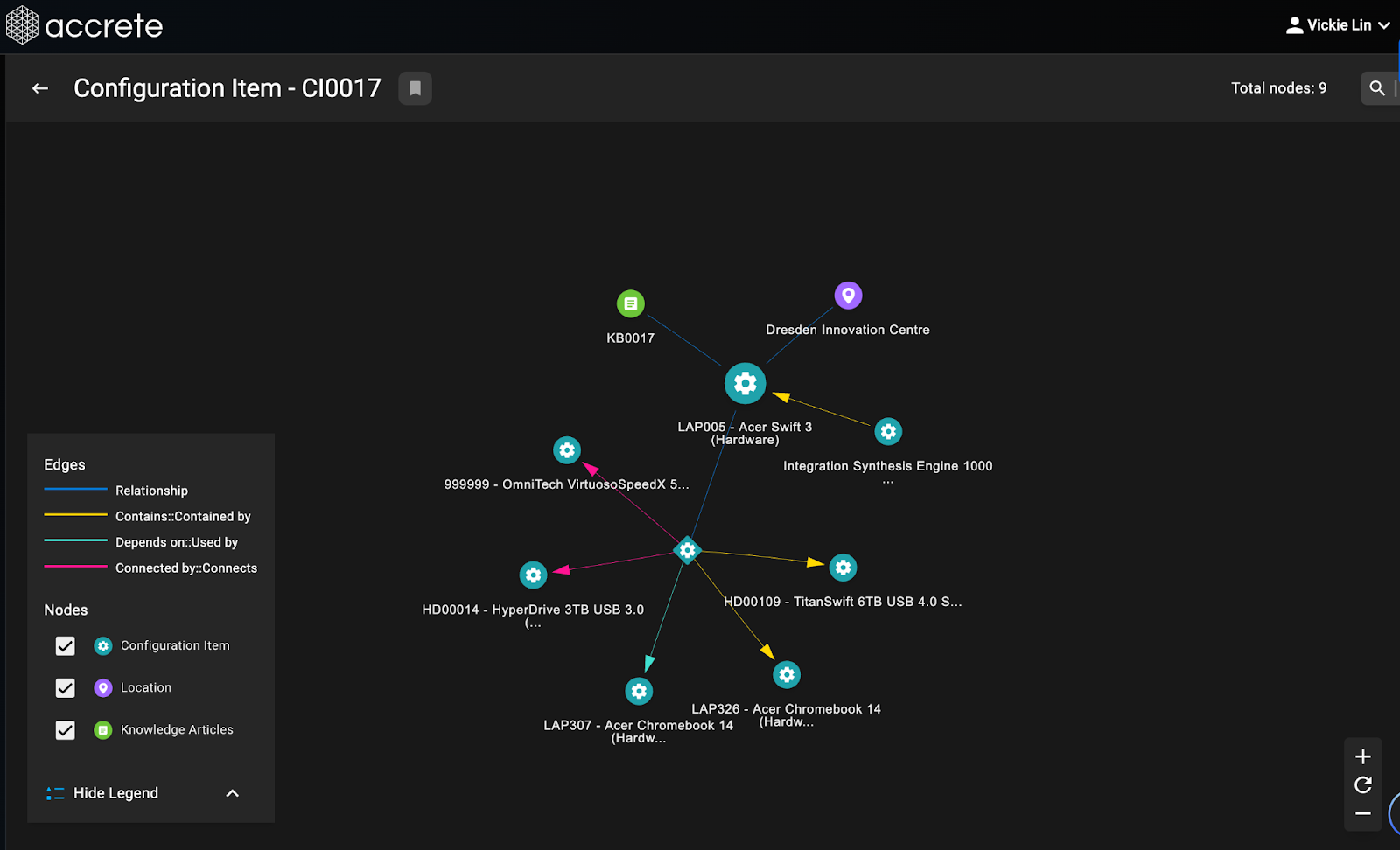
When a change owner looks at a specific knowledge graph around a particular configuration item, they can also view all of the upstream and downstream Configuration Items and all their related data such as incidents (orange icons), change tickets (pink icons), and so on. Being able to show all of this data is essential to change ticket risk assessment; understanding the business impacts of taking a Configuration Item offline. Once we have all of this interconnected change management data, Accrete’s Nebula ITSM tool can then start to analyze historical data to capture lessons learned for IT change planning.
- Workflow automation: AI-based systems could potentially route change requests automatically to the right stakeholders, eliminating time lost coordinating manually. Such systems can determine the prioritization of requests depending on their urgency and potential impact that can address critical changes quickly.
- Policy compliance: AI can also be used to ensure that all proposed changes have support from internal policies and industry regulation. It automatically cross-references change requests with regulatory requirements, avoiding changes indicated as having possible non-compliance and thus slowing probable legal or operational implications.
In summary, AI is revolutionizing change management in manufacturing with tools like Accrete AI’s Nebula ITSM platform, but more critically, where IT and OT are converging and risks at stake are high. Embedded within AI is deterministic risk prediction and approval process automation, which provides manufacturing companies with the capability to implement change more quickly while de-risking the change process. This not only enhances the manufacturing company's overall IT operational efficiencies but would also be a competitive advantage as the fast-evolving manufacturing landscape unfolds.